Advanced Propulsion Concepts
Solar Thermal Propulsion
The Air Force and NASA chose rhenium for their solar thermal propulsion systems because of its high melting point and excellent
ductility. In these systems, sunlight is focused into a rhenium blackbody heat exchanger, and the solar energy heats the hydrogen. The heated hydrogen propellant is then exhausted through a nozzle to produce thrust with a specific impulse of up to 1000 seconds.
Rhenium foam was used for the heat exchanger because of its excellent ductility, strength at temperature, high surface area, and ease of fabrication. Furthermore, to ensure that the cavity had the optical performance of a true blackbody, the interior of the cavity was coated with black rhenium.
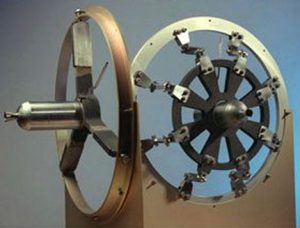
Solar thermal thrusters. Rhenium foam is used for support structures to accommodate thermal expansion and minimize parasitic heat loss to the main structure.
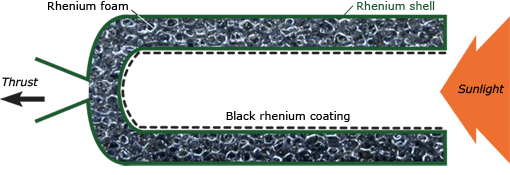
Solar thermal rocket engine